Well, it has been a while. I thought it would be good to let everyone know how this all ended. Back in 2015 the boat was sitting at about 98% completion, and then I went through a divorce. I received the boat in the divorce, but I did not have a place to work on it, and the funds were low. A guy offered to put the outdrove on for me for $400 but he just took the money and never finished the work. The boat sat for another year before my financial situation got so bad I had to sell her very cheap.
I was heartbroken to sell her, but I knew it was going to a better place. She is up noth and is at the large Classic Glastron meet every year. The new owner sent me some pictures of her finished so that I can conclude this series.
Thanks to all the fans that watched the build, and I hope this brings some closure. Make sure you check out the video for alot more detail.
FriscoBoaters's 1986 Glastron Carlson CVX-18 Restoration
Restoring a completely rotten Glastron Carlson CVX-18. This includes all pictures and videos.
Wednesday, September 18, 2019
Sunday, March 10, 2013
Gel Coat Repair and polishing
Its is time for another large update. I feel it has taken me forever to get the polishing and gel coat repairs done. It is a very long a tedious process, but the results are just stunning. I had never done gel coat repair before, and the first time I failed bad, but after a try or two I figured it out. I am very happy with the results, and would tackle it again in the future for sure.
So lets get down to the details.
The first thing I had to do is get the old stickers off along with the pinstripes. I first used tracing paper to make an impression of the sticker on the bow so that I can get it reproduced. I then used a 3M eraser wheel to remove the pinstripes and any stickers left on the boat. The eraser worked really nice to remove the stripes with ease.
This is the wheel I used



I then started the sanding process. I wanted to get the sanding and one stage of polishing done so that I could see just where I needed to repair the gel coat.You want to remove just enough material to get rid of the oxidation, and no more. I started with 600 grit in most places, then 800, then, 1000, then 1500 to get rid of the 600 grit sanding scratches. The idea is to progressively get finer and finer with your grit until you have a mirror shine.
This is after the three steps of sanding. You will see it is pretty dull.. but don't panic.


Once you have finished the sanding steps, you will start with a wool buffing wheel and a fairly course compound to further get rid of the sanding scratches.

Dad tried his hand at polishing too. It is a craft you really have to practice to get right.

You can see that the shine is starting to come back now. This is only after one of the 4 or 5 polishing steps.

Now it was time for the stuff I had never done before... gel coat repair. I had several deep gouges in the grey and the black glitter, so I had to get them filled and gel coated. Plus I had sanded through a few places, and they need a re-spray.
What I did first was mix up the right color gel ( and that took forever with the grey) and then thicken it up like Peanut Butter so that I could putty the gouges. You want to leave the repair a little higher than the hull, and then once it cures you sand it level with the surface. You could polish and be done, but I wanted to bland it better.
This was a large gouge here and this is after the filler has been added.

These were two deep holes that I filled. You can see where I sanded through here.

Once that was done I mixed up black non waxed gel coat, thinned it with 10% Styrene thinner and sprayed it through my small detail gun. I feathered the edges out to kinda blend the black.

I then took non waxed clear gel coat and mixed in my metal flake that I found from PPG. All I was trying to do was to get a decent pattern here. The idea is to vary your spray pressure and distance to get the flak to lay in deferent ways.

The next step was to lay down a thinned out layer of non waxed black over the metal flake to dull it down a bit. By doing this it makes the flak look like it is deeper in the black, not laying right on top. It makes them shimmer differently. Over that coat i did the clear mixed with metal flake again, and that gave me my desired effect. Once that cured, I went over it with Clear gel mixed with patch booster. Patch booster is like wax, but also thins out the clear much more, and boosts the gloss a bit. This is the final layer would will be polishing. I found that is I put standard wax in the clear, it got cloudy. The patch booster fixed that.
Remember to feather your spraying farther over each coat. A one inch repair could have a 12" diameter feather out.
This is after the final clear coat. You can see that the gel coat has alot of orange peel, and that is almost unavoidable. I put down seven coats of clear, and will sand off 2 for polishing.



Once it cured for about 5 hours, I took 320 to it to level out the orange peel, and then started the other sanding and polishing procedure.
This is what it should look like.



No more gouges or holes!
Once I had tackled that black repairs, I hit the grey areas. I had a bunch of scraps and gouges all over the place, and it took me hours to fix them all.





Here is a good shot of Dad hitting the lower side of the hull with 800 grit

After the beating of doing all the repairs, we finished up the polishing. We had already done the wool bonnet stage, so now we went over it with a yellow pad, and the same polish we used with the wool. Once that was complete we went over it with a grey foam pad and super fine polish for a really nice shine. The I stuck a coat of wax on it, stepped back and almost shed a tear. I would have never thought this poor boat could look this good.



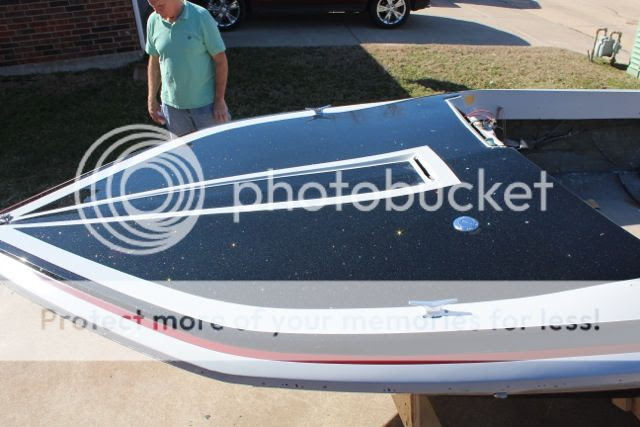




Here is all of the stuff that I used in the polishing of this boat. It is a sizable investment, but the results speak for themselves.

Now for all of the videos
So lets get down to the details.
The first thing I had to do is get the old stickers off along with the pinstripes. I first used tracing paper to make an impression of the sticker on the bow so that I can get it reproduced. I then used a 3M eraser wheel to remove the pinstripes and any stickers left on the boat. The eraser worked really nice to remove the stripes with ease.
This is the wheel I used
I then started the sanding process. I wanted to get the sanding and one stage of polishing done so that I could see just where I needed to repair the gel coat.You want to remove just enough material to get rid of the oxidation, and no more. I started with 600 grit in most places, then 800, then, 1000, then 1500 to get rid of the 600 grit sanding scratches. The idea is to progressively get finer and finer with your grit until you have a mirror shine.
This is after the three steps of sanding. You will see it is pretty dull.. but don't panic.
Once you have finished the sanding steps, you will start with a wool buffing wheel and a fairly course compound to further get rid of the sanding scratches.
Dad tried his hand at polishing too. It is a craft you really have to practice to get right.
You can see that the shine is starting to come back now. This is only after one of the 4 or 5 polishing steps.
Now it was time for the stuff I had never done before... gel coat repair. I had several deep gouges in the grey and the black glitter, so I had to get them filled and gel coated. Plus I had sanded through a few places, and they need a re-spray.
What I did first was mix up the right color gel ( and that took forever with the grey) and then thicken it up like Peanut Butter so that I could putty the gouges. You want to leave the repair a little higher than the hull, and then once it cures you sand it level with the surface. You could polish and be done, but I wanted to bland it better.
This was a large gouge here and this is after the filler has been added.
These were two deep holes that I filled. You can see where I sanded through here.
Once that was done I mixed up black non waxed gel coat, thinned it with 10% Styrene thinner and sprayed it through my small detail gun. I feathered the edges out to kinda blend the black.
I then took non waxed clear gel coat and mixed in my metal flake that I found from PPG. All I was trying to do was to get a decent pattern here. The idea is to vary your spray pressure and distance to get the flak to lay in deferent ways.
The next step was to lay down a thinned out layer of non waxed black over the metal flake to dull it down a bit. By doing this it makes the flak look like it is deeper in the black, not laying right on top. It makes them shimmer differently. Over that coat i did the clear mixed with metal flake again, and that gave me my desired effect. Once that cured, I went over it with Clear gel mixed with patch booster. Patch booster is like wax, but also thins out the clear much more, and boosts the gloss a bit. This is the final layer would will be polishing. I found that is I put standard wax in the clear, it got cloudy. The patch booster fixed that.
Remember to feather your spraying farther over each coat. A one inch repair could have a 12" diameter feather out.
This is after the final clear coat. You can see that the gel coat has alot of orange peel, and that is almost unavoidable. I put down seven coats of clear, and will sand off 2 for polishing.
Once it cured for about 5 hours, I took 320 to it to level out the orange peel, and then started the other sanding and polishing procedure.
This is what it should look like.
No more gouges or holes!
Once I had tackled that black repairs, I hit the grey areas. I had a bunch of scraps and gouges all over the place, and it took me hours to fix them all.
Here is a good shot of Dad hitting the lower side of the hull with 800 grit
After the beating of doing all the repairs, we finished up the polishing. We had already done the wool bonnet stage, so now we went over it with a yellow pad, and the same polish we used with the wool. Once that was complete we went over it with a grey foam pad and super fine polish for a really nice shine. The I stuck a coat of wax on it, stepped back and almost shed a tear. I would have never thought this poor boat could look this good.
Here is all of the stuff that I used in the polishing of this boat. It is a sizable investment, but the results speak for themselves.
Now for all of the videos
Putting the Cap back on
It is update time again. It has been tough to find time to work on the boat alot the past couple of weeks, much less update the thread and website. Things are really coming together, and I can see the light at the end of the tunnel.
I am going to change the thread format a little and type what I am doing above the pictures to help dictate what is going on better. As I mentioned before, I will most likely be doing gel coat all inside the boat and then using hydroturf glued in as mats. I think this is the best of both worlds and will give the new owner a slick updated look, and if they choose to put down carpet... they can. More to come on this.
So here we go.
We needed to get the gas tank structure built... so Dad and I rigged up a nice system to raise and lower the cap so we could check fitment. I just used a 1/2 ton hoist screwed into the joint and it allowed me to raise and lower with ease.


We used the cleats to tie the rope to.

I then assembled the old tank structure (see why I kept it) and put it back in to make sure it still fit... which it did.

I then tore it back down again and then traced all the patterns on the new wood and cut it out.

One I had all the pieces cut I had to glue the 2X3 pieces of wood down to the deck that form the structures base. I used Peanut butter (thickened resin) to do this and then used some weight to hold it down. These will also get glassed later.

After treated the end grains with several coats of slow kick resin (resin mixed to cure slowly so it soaks in) I used Peanut butter again to glue and screw the sides to the bases. I used 1708 on the outside and the inside of the base to really hold it to the deck.

Once that cured I put down teh gas tank floor that had been coated in resin and one layers of CSM. I like using CSM on boards that will be sitting flat. The CSM really adds that extra water protection. Boards that are not structural, and are vertical, I usually just tab in and then coat in resin and then paint of gel. The water will run right off this.
I glues and screwed the floor in also and then tabbed with 1708.

Once teh resin cured I rolled on two coats of rustoleum grey to give the structure and nice look.



I also cut out the transom hole with a Dremel tool. I still need to drill the steering relief holes, but I will do that soon.

I have alos started working on the wiring for the boat. I know it looks like a mess, but I know what is going on. The wiring is actually very usable, and will cut down on time. I fellow boater and fan has graciously made me a great deal on some gauges for the boat!

I also discovered that the Steering is shot, and I will have to get a full new rack. Soooo the steering got ripped out.

I was happy to find out that the instrument cluster can be buffed to a shine. It is that clean circle on the left. One of the videos shows it better.

With a new fuel sender installed, the gas tank is back in her resting spot. I used pieces of recycled tire floor mat cut into pieces for the padding.

We decided to put carpet up front as it will cut down on water noise and if you put skis up there is will keep them from banging the hull. This stuff was a pain in the butt to lay down, but we got it. You really will never see this, and i personally hate the way it turned out.

Now it was time to build the kick plate that the driver and passenger rest their feet on. We used foam to make a template of the bottom first as the original was ruined.

The top area was a different story... as I was able to use the original as a template.. YEAH!!


Once it was done and all test fitted, it was time to cut it out of wood.

Once we got the wood cut and got the rough shape cut out it was time to get it mounted in.

I needed a way to secure the kick plate down without screwing to anything permanent. So what i did is make a sacrificial mounting structure that I glued in for the kick plate to screw too.

I cut out the middle so that water could run out, and made an indention on the back of the kick plate so that the water did not get trapped.

Once that was dry, I screwed the kick plate down and then used peanut butter all around it... with the exception of the lower front. This will allow water to escape from the front it it gets there. Notice teh green stuff there. I ran out of cabosil to make Peanut butter, and used Bondo glass. It was terrible, and kicked off in about 5 minutes.


I will tab all of this in after I get more cabosil and can make some more smooth peanut butter and make the seams smoother.
Thats it for the pictures on this update. Now here is about an hour of video that goes into more detail.
I am going to change the thread format a little and type what I am doing above the pictures to help dictate what is going on better. As I mentioned before, I will most likely be doing gel coat all inside the boat and then using hydroturf glued in as mats. I think this is the best of both worlds and will give the new owner a slick updated look, and if they choose to put down carpet... they can. More to come on this.
So here we go.
We needed to get the gas tank structure built... so Dad and I rigged up a nice system to raise and lower the cap so we could check fitment. I just used a 1/2 ton hoist screwed into the joint and it allowed me to raise and lower with ease.
We used the cleats to tie the rope to.
I then assembled the old tank structure (see why I kept it) and put it back in to make sure it still fit... which it did.
I then tore it back down again and then traced all the patterns on the new wood and cut it out.
One I had all the pieces cut I had to glue the 2X3 pieces of wood down to the deck that form the structures base. I used Peanut butter (thickened resin) to do this and then used some weight to hold it down. These will also get glassed later.
After treated the end grains with several coats of slow kick resin (resin mixed to cure slowly so it soaks in) I used Peanut butter again to glue and screw the sides to the bases. I used 1708 on the outside and the inside of the base to really hold it to the deck.
Once that cured I put down teh gas tank floor that had been coated in resin and one layers of CSM. I like using CSM on boards that will be sitting flat. The CSM really adds that extra water protection. Boards that are not structural, and are vertical, I usually just tab in and then coat in resin and then paint of gel. The water will run right off this.
I glues and screwed the floor in also and then tabbed with 1708.
Once teh resin cured I rolled on two coats of rustoleum grey to give the structure and nice look.
I also cut out the transom hole with a Dremel tool. I still need to drill the steering relief holes, but I will do that soon.
I have alos started working on the wiring for the boat. I know it looks like a mess, but I know what is going on. The wiring is actually very usable, and will cut down on time. I fellow boater and fan has graciously made me a great deal on some gauges for the boat!
I also discovered that the Steering is shot, and I will have to get a full new rack. Soooo the steering got ripped out.
I was happy to find out that the instrument cluster can be buffed to a shine. It is that clean circle on the left. One of the videos shows it better.
With a new fuel sender installed, the gas tank is back in her resting spot. I used pieces of recycled tire floor mat cut into pieces for the padding.
We decided to put carpet up front as it will cut down on water noise and if you put skis up there is will keep them from banging the hull. This stuff was a pain in the butt to lay down, but we got it. You really will never see this, and i personally hate the way it turned out.
Now it was time to build the kick plate that the driver and passenger rest their feet on. We used foam to make a template of the bottom first as the original was ruined.
The top area was a different story... as I was able to use the original as a template.. YEAH!!
Once it was done and all test fitted, it was time to cut it out of wood.
Once we got the wood cut and got the rough shape cut out it was time to get it mounted in.
I needed a way to secure the kick plate down without screwing to anything permanent. So what i did is make a sacrificial mounting structure that I glued in for the kick plate to screw too.
I cut out the middle so that water could run out, and made an indention on the back of the kick plate so that the water did not get trapped.
Once that was dry, I screwed the kick plate down and then used peanut butter all around it... with the exception of the lower front. This will allow water to escape from the front it it gets there. Notice teh green stuff there. I ran out of cabosil to make Peanut butter, and used Bondo glass. It was terrible, and kicked off in about 5 minutes.
I will tab all of this in after I get more cabosil and can make some more smooth peanut butter and make the seams smoother.
Thats it for the pictures on this update. Now here is about an hour of video that goes into more detail.
Subscribe to:
Posts (Atom)